Lean Erfahrungsbericht, der begeistert
Not und Krisen machen bereit für Veränderungen zum Besseren (KaiZen). Lean-Methoden bringen Verbesserungen.
Die Kaizen-Kultur stammt aus Japan. Dort entstanden bei Toyota die Lean-Methoden der Fertigung. Denn Japan war nach dem Zweiten Weltkrieg ein zerstörtes, rohstoffarmes Land, welches kein Geld, aber Heerscharen arbeitssuchender Menschen hatte. Dieses Land hatte nach dem verlorenen Krieg definitiv große Not und war in einer existentiellen Krise. Es wurde zu einer der Top-3-Industriemächte der Erde. Um auch ohne Marshallplan mit ihrer Industrie wieder auf die Beine zu kommen, entwickelten die Japaner in ihrer Not Methoden für die Fertigung, für deren Wirkung später im Amerikanischen der Sammelbegriff „Lean“ gefunden wurde.
Taiichi Ohno ist der Urvater von „Lean“. Er entwickelte in den Jahrzehnten nach dem Krieg bei Toyota 37 Prinzipien bzw. Methoden für hohe Produktivität und Qualität in der Fertigung. Dies war die Basis für das berühmte Toyota Production System (TPS). Es definiert das Arbeitsumfeld für Menschen in der Produktion. Der Titel seines ersten Buches lautet deshalb auch „Taichii Ohno’s Workplace Management“. Es wurde zum weltweit bekannten Kaizen-Grundlagenwerk mit 37 Kapiteln und nur 200 Seiten. Daraus haben besonders US-Autoren viele dicke „Lean“-Büchern für alle Bereiche des Lebens abgeleitet.
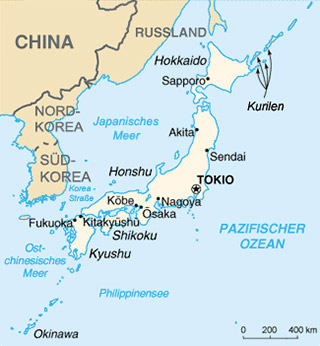
Das „Lean“-Basiswerk
Meine Krisen und Notlagen
Mein erste vitale Krise und Notsituation erlebte ich mit 31 Jahren. Von den USA aus wechselte ich zu einem neuen Arbeitgeber. Am ersten Arbeitstag begrüßte mich ein Sanierer der kreditgebenden Banken anstelle des geschäftsführenden Alleingesellschafters. Die Belegschaft war von 260 auf 215 Leute zusammengestrichen worden. Die guten Leute waren im Jobsuchmodus. Mein designierter Vorgesetzter war gefeuert und ich wurde am ersten Arbeitstag vom Sanierer als sein Nachfolger benannt. Ich war neu in der Branche und kannte die Technik (Motion Control) überhaupt nicht. Verkäufer hatte ich auch noch nicht geführt.
“… Jürgen took his responsibility at an economically very difficult point in time for the company. Re-Structuring … had become essential …“
Zitat aus Arbeitszeugnis nach fünf Jahren Arbeit bei Hauser Elektronik/Parker Hannifin
Auch die halbjährlichen Reviewmeetings mit den kreditgebenden Banken und die freitäglichen Runden des Cash-Notmanagements waren für mich neu.
Geld für Berater war keines vorhanden. Unter diesem Druck entwickelte ich zwei einfache und schnell „Lean-Führungsinstrumente“, um meine berufliche Karriere nicht schon mit 31 Jahren scheitern zu sehen. Von Lean und Kaizen hatte ich damals noch nichts gehört. Ich ließ im Vertrieb, Applikations- und Feldsupport einfach alles weg, was nicht wertschöpfend war, und setzte auf einfachste Mittel mit geringster Komplexität.
Mit Fertigung hatte ich damals noch nichts zu tun.
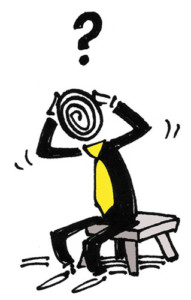
Guter Rat ist teuer. Darum eigenen Kopf und Leute nutzen.
Bei Hauser Elektronik war ich 1992 in beruflicher Überlebensnot. Acht Jahre später war ich als junger Familienvater wieder in einer ähnlichen Situation. Im Frühjahr 2000 bekam ich bei Saia-Burgess in Murten (CH) eine ausgemergelte, kranke Cash Cow mit akuter Gefahr des Exodus zur Rettung übergeben. Bei unvermindert guter Profitabilität sollte eine Sanierung oder ein schneller Verkauf erfolgen.
Bei Misserfolg wären meine Karriere bei Saia-Burgess und mein Aufenthalt in der Schweiz schnell zu Ende gewesen.
Zwei Lean-Führungsinstrumente aus der Hauser-Erfahrung halfen mir bei der Bewältigung der Aufgabe. Eine drittes Führungsinstrument in Form eines verblüffend einfachen Navigationssystem für Mitarbeiter (KlarNet) entstand ab 2001.
Lean-Erfahrung hilft bei Kostendruck durch Eurokrise und Billiglohnländer
Ab 2006 wechselte mein Arbeitsschwerpunkt zur Produktion. Die Kundenseite des Unternehmens entwickelte sich gut. Neue Produkte und Technologien wurden reif für die Produktion. Aber die seit Jahrzehnten praktizierte Form der Produktion erwies sich als zu langsam, zu unflexibel und zu teuer. Unsere Brand-Label-Kunden bauten immer mehr Produktionskapazität in China und Osteuropa auf. Wir wurden in Konkurrenz mit Niedriglohnländer gesetzt.
Ohne massive Steigerung der Konkurrenzfähigkeit drohte ein Drittel des Produktionsvolumens verloren zu gehen. In dieser angespannten Lage kam der massive Wechselkursverlust des Euro gegenüber dem Schweizer Franken hinzu. Es entstand eine chronische Krise.
Ich begann mich mit dem Begriff „Lean“ zu befassen. Im Jahr 2007 machte ich ein Genba-Kaizen-Praxisseminar in japanischen Werkshallen. Das veränderte mein berufliches Leben und meine Denkweise nachhaltig. Es sorgte für einen Bruch mit alten Paradigmen in meinem Kopf.
Eine Führungskraft der Produktion beschreibt den Start mit japanischem Lean bei Saia-Burgess Controls.
Diese Kunden nahmen ein Drittel unseres Produktionsvolumens an Elektronikgeräten ab. Jeder hatte selbst eine Produktion im Euroraum und vielfach auch in Osteuropa/China.
Der Schweizer Franken wurde zu Fluchtwährung. Der Wechselkurs stürzte in vier Jahren von 1,67 auf 1.20 ab.
Die Mitarbeiter arbeiten volle Kraft. Quantensprünge an Produktivität sind nur mit andere Arbeitsmethodik möglich. Wir brauchten die japanischen Genba-Kaizen-Methoden.
Bis 2009 durchlief die gesamte Führungsmannschaft der Saia-Burgess Controls AG diese Kaizen-Seminare in Japan organisiert vom Kaizen Consulting Unternehmen Shingijutsu in Nagoya). Ab 2010 ließen wir die Kaizen-Meister zweimal im Jahr für mehrtägige Workshops aus Japan einfliegen.
Der Meister Moro San beim Genba-Kaizen-Workshop im Werk in der Schweiz. Er sprach nur Japanisch. Er war hoch geachtet und beliebt.
Sukzessive Umstellung der ganzen Produktion auf Zellen, one piece flow und Pull-Prinzip bis in die dezentralen Auslieferlager an Kunden.
Die emotionale Achterbahnfahrt beim japanischen Genba-Kaizen-Workshop. Es sind radikale, disruptive Veränderungsschritte auch über die Grenze der Komfortzone der Beteiligten hinweg.
Lean-Erfahrung:
Die positive Wirkung der eigentlich sehr einfachen Prinzipien und Methoden aus Japan war überwältigend. Auch die Produktions-Overheadkosten sanken gewaltig.
Taiichi Ohno’s Workplace Management wirkt in der Schweiz Wunder
Mit der Nutzung der Lean-Methoden in der Produktion hatten wir großen Erfolg. Die Volumenkunden konnten gehalten werden. Der Effekt des schwachen Euros wurde kompensiert. Das war nur möglich, weil wir das in der Produktion Gelernte konsequent in allen Unternehmensbereichen anwendeten. Zwei neue Methoden für Lean-Arbeiten von Kopfarbeitern entstanden (2ease.SMap, 2ease.SInfo).
Damit stieg die Produktivität nicht nur in der 80-köpfigen Produktion, sondern bei allen 350 Mitarbeitern.
Um ein Gefühl für die wundersame Wirkung einfacher Methoden zu vermitteln, ließen wir alle Mitarbeiter als „Gastarbeiter“ 2-3 Stunden in der Produktion arbeiten. Nach 20 min Einarbeitung konnten jedermann dank der intuitiven, einfachen Gestaltung der Produktionszellen (Workplace) verpackte und voll verkaufsfähige Produkte wie Energiezähler und SPS-Steuerungen herstellen.
Sehen und hören Sie, wie er seine Lean-Erfahrung empfunden hat.
Auch Journalisten kamen gerne zur Lean-Produktionserfahrung nach Murten
Praktische Lean-Erfahrung: Kunden kamen ins Schweizer Werk, um ihre Steuerungen und Energiezähler selbst herzustellen. ☺
Die A5 Abschiedskarte vom 28.2.2014 zeigt, wie stark das japanische Lean das gesamte Unternehmen Saia-Burgess Controls geprägt hat.
Herr Endress vom 1.8 Mrd. Euro Unternehmen Endress+Hauser mit einem seiner Werksgeschäftsführer nach seinem erfolgreichen 45-minütigen Produktionseinsatz.
Der damalige CEO des 11 Mrd. CHF Unternehmens Swisscom mit seinem CTO nach seinem erfolgreichen 45-minütigen Einsatz als Arbeiter.
Lean-Erfahrung überall – einfache Methoden und Prinzipien für den Betrieb eines gesamten Unternehmens
Wie hat der externe ISO 9001 Auditor der Schweizer Gesellschaft für Qualitätssicherung (SQS) über ein Jahrzehnt die Transformation der Saia-Burgess Controls zum Lean Enterprise empfunden?
Was hat sich im QM-System seit der Umstellung auf Lean-Produktion verändert?
Mit der Einführung der Lean-Prinzipien ins bestehende Managementsystem haben sich in zahlreichen Prozessen Veränderungen ergeben. So wurden die Prozesse analysiert und allfälliger «Ballast» abgeworfen und an der Effizienzsteigerung gearbeitet. Dies hat dazu geführt, dass die Prozesse meist anders dargestellt und die «One-Piece-Flow-Prinzipien» eingebaut wurden.
Was haben Sie von der Veränderung von Saia-Burgess hin zu einem Lean- Unternehmen gespürt?
Nebst den oben genannten Fortschritten fällt auf, dass in allen Prozessen «Lean» ein Thema ist und nicht nur bei den Wertschöpfungsprozessen (z. B. im Complaint Handling).
HR/Finanzchef: Seine Erfahrungen mit Lean?
Ein Professor von der Universität St. Gallen mit Schwerpunkt Enterprise 2.0 interviewt nach einem Werksbesuch bei Saia-Burgess Controls AG den HR/Finanzchef Adrian Spicher und den Geschäftsführer Jürgen Lauber.
Wie sehen die neuen Eigentümer Honeywell die Lean-Betriebsweise, die sie bei Saia-Burgess Controls in Murten vorfanden?
Auszug aus einem Schreiben des Integrationsleiters für die „Operation“ Dr. Arenz, Honeywell:
„ … Als Verantwortlicher für den Bereich Operation habe ich einen guten Einblick in „Ihr“ früheres Unternehmen bekommen, speziell in zwei flexible, schlanke und effiziente Fertigungsstätten in Murten, die stabil und in hoher Qualität und Service liefern.
Beeindruckt hat mich die nachhaltige und tiefgehende Verankerung des Lean-Produktionssystems bei praktisch allen Mitarbeitern. Sie haben hier in Murten in einer besonderen Weise japanische Produktionsmethoden mit neuester Technologie verknüpft. So beschränken sich die „Saia Lean-Prinzipien“ nicht nur auf die Fertigung selbst, sondern es finden sich viele Elemente und einheitliche Standards auch in vielen Prozessen anderer Bereiche, wie z. B. Entwicklung, Produktmanagement, Verkauf oder unterstützender Funktionen. Diese Kombination wirkt sich positiv auf Leistung und Stimmung im Personal aus… Auch nach Ihrem Ausscheiden als Geschäftsführer wird diese Kultur im Unternehmen weiter gelebt und das beweist, wie stark die Mitarbeiter diese Kultur als den „für sie richtigen Weg“ verinnerlicht haben. …“
Auszug aus Artikel von ControlsNew 13 CN13_DS_S23.pdf
Im März 2014 schreibt mir mein Honeywell-Nachfolger als Geschäftsführer folgendes:
1) Wir haben ein Unternehmen gefunden, welches sehr schlank und robust organisiert ist. Auch ohne den gewohnten Chef hat das Unternehmen unter neuen Umständen reibungslos und effizient weiter gearbeitet.
2) Das Managementsystem und die besonderen Management-Methoden der Saia-Burgess Controls werden auch in Zukunft weiter geführt. Teile daraus werden sogar in das Honeywell System übernommen.
Persönliche Abschlussbemerkung: Es kann für mich kein schöneres Kompliment geben, als die Bestätigung der beiden Honeywell Manager, dass auch ohne Management das Unternehmen sicher und effizient weiter funktioniert.
Ausblick: Die bei Saia-Burgess Controls entwickelten Methoden für den Lean-Betrieb des ganzen Unternehmens haben inzwischen auch in der Forschung und Lehre Widerhall gefunden.
Ein Wirtschaftsinformatik-Lehrstuhl der Uni St. Gallen hat darüber auch schon eine Fallstudie im Kontext von Enterprise 2.0 veröffentlicht.
Es gibt darüber ein Kapitel in einem kürzlich erschienen Buch über vernetzte Organisationen.
Mit dem Fokus Unternehmens Kaizen wird 2015 die 2ease AG aufgebaut.
Damit die Kaizen-Grundgedanken von Taiichi Ohno für Einzelpersonen und auch gesamte Unternehmen wundersamen Wirkung entfalten, gibt es die 2ease Führungsinstrumente. Damit kann man sich selbst und andere sicher und einfach ( easy) zum Besseren führen.
Brief von Honeywell Nachfolger, Ernst Malcherek.
Buch mit einem Kapitel über die Saia-Burgess Controls Lean-Methoden in der Informationslogistik und Kooperation.
Es war mir eine Freude, eine Gastvorlesung an der Uni St. Gallen zu halten.
Das Thema war: Wie kann einfach und ohne Risiko der Unternehmensgewinn um 2-3 Prozentpunkte erhöht werden?